En el mundo industrial, pocas cosas son tan costosas y frustrantes como una parada inesperada de producción. A menudo, el origen de esos problemas puede encontrarse en elementos aparentemente simples: las válvulas de control y sus sellos. Una válvula mal mantenida o un sello deteriorado puede provocar desde fugas menores hasta fallos catastróficos que paralizan líneas enteras.
En este artículo analizamos cinco señales claras de fallos en válvulas o sellos, y te explicamos cómo prevenir interrupciones no planificadas que afectan la rentabilidad, seguridad y eficiencia de tu planta.
1. Fugas visibles: la alerta que no puedes ignorar
Una de las señales más evidentes de que algo está mal es la aparición de fugas visibles de fluido alrededor de la válvula, el vástago o las conexiones.
¿Qué lo causa?
Las fugas visibles alrededor de una válvula son casi siempre el síntoma de una degradación interna progresiva. Para entender su origen —y evitar que escalen a una falla crítica— es clave conocer las causas más frecuentes:
Desgaste en los empaques o sellos
Los sellos (empaques, juntas tóricas, anillos de grafito o PTFE) están diseñados para resistir presión, temperatura y contacto con fluidos agresivos. Sin embargo, con el tiempo sufren:
- Fatiga mecánica, por la constante apertura/cierre de la válvula.
- Aplastamiento permanente, que reduce su capacidad de sellado.
- Degradación química, cuando el fluido de proceso es corrosivo o incompatible con el material del sello.
- Envejecimiento térmico, que cristaliza o endurece materiales blandos, volviéndolos quebradizos.
Un empaque fatigado puede comenzar a permitir filtraciones intermitentes, que muchas veces no se detectan hasta que se convierten en una fuga visible.
Mal ajuste del vástago o asiento
El vástago (stem) conecta el actuador con el obturador de la válvula, y debe moverse alineado y con precisión. Sin embargo:
- Una instalación incorrecta o desalineada puede generar roce desigual y desgaste prematuro.
- Golpes de ariete o picos de presión pueden deformar ligeramente el vástago, generando fricción o juego.
- El asiento (seat), donde cierra el obturador, también puede estar mal mecanizado o dañado, impidiendo un cierre hermético.
Esto produce microfugas que aumentan con cada ciclo, provocando pérdida de estanqueidad y esfuerzos mecánicos innecesarios.
Corrosión interna en el cuerpo de la válvula
Las válvulas instaladas en líneas de vapor, químicos, aguas con alto contenido de cloruros o fluidos ácidos están especialmente expuestas a:
- Corrosión por picado, que genera microperforaciones en el cuerpo o tapa.
- Corrosión galvánica, si hay contacto entre metales diferentes en presencia de un electrolito.
- Despasivación de aceros inoxidables por presencia de cloruros o temperatura elevada, lo que acelera la oxidación interna.
Esta corrosión puede adelgazarse hasta perforar el cuerpo, o generar acumulaciones internas que desalinean el movimiento de cierre.
¿Por qué es grave?
Una fuga que parece “pequeña” puede:
- Provocar pérdida de producto.
- Generar riesgos de seguridad (químicos, vapor, presión).
- Ser indicio de fallas mayores en desarrollo.
Cómo prevenirlo
- Realiza inspecciones visuales cada semana en válvulas críticas.
- Usa sensores de detección de fugas para líneas peligrosas o de difícil acceso.
- Sustituye empaques y juntas antes de su vida útil estimada.
- Instala válvulas con certificación de estanqueidad adecuada al tipo de fluido (API, ISO 5208, etc.).
TE PUEDE INTERESAR – Refacciones para bombas y válvulas sanitarias
2. Vibraciones anormales: una amenaza silenciosa
¿Escuchas o sientes una vibración irregular en una línea de proceso? No lo ignores. Las vibraciones mecánicas son un síntoma claro de mal funcionamiento hidráulico o estructural.
Posibles causas
- Desgaste en el eje o asiento de la válvula.
- Cavitación interna por baja presión aguas abajo.
- Flujo turbulento no controlado.
- Desalineación de la válvula con la tubería.
Riesgos asociados
- Desgaste acelerado de componentes móviles.
- Daño estructural en tuberías y soportes.
- Ruido excesivo y pérdida de eficiencia hidráulica.
- Desajuste progresivo en actuadores neumáticos o eléctricos.
¿Cómo actuar?
- Revisa que el dimensionamiento hidráulico (Cv) sea adecuado para el caudal real.
- Utiliza válvulas con geometría de paso optimizada y protección anti-cavitación.
- Incluye sensores de vibración en sistemas críticos.
- Realiza análisis de firma vibracional para prever fallas internas.
3. Fallos en el cierre o apertura total: precisión en juego
Una válvula que no abre ni cierra por completo es un problema común que compromete la precisión del control de flujo y presión en cualquier proceso industrial.
Causas probables
- Acumulación de residuos o incrustaciones en el trim
- Sellos deformados por temperatura o presión excesiva
- Fallas en el actuador o pérdida de señal de control
- Fricción excesiva por falta de lubricación
Consecuencias operativas
- Flujo insuficiente o descontrolado
- Desbalance hidráulico en líneas paralelas
- Saturación de otros componentes (bombas, intercambiadores)
- Impacto negativo en la calidad del producto final
Soluciones prácticas
- Implementa rutinas de limpieza y purgado del trim.
- Recalibra periódicamente los actuadores.
- Lubrica el vástago y componentes móviles con productos adecuados.
- Considera válvulas de control con posición de diagnóstico y monitoreo integrado.
4. Tiempos de respuesta lentos o erráticos: eficiencia en riesgo
El rendimiento de una válvula no se mide solo por su capacidad de abrir o cerrar, sino por cuán rápido y preciso lo hace. Un comportamiento lento o inconsistente puede causar desajustes serios en el proceso.
Indicadores clave
- El controlador emite una orden, pero la válvula tarda segundos en responder
- Cambios de posición incompletos
- Inestabilidad en la presión o temperatura del sistema
Origen posible
- Baja presión de suministro neumático
- Desgaste en los componentes internos del actuador
- Fugas internas que reducen la capacidad de control
- Obstrucciones o residuos en el paso
Estrategias de mantenimiento
- Verifica y calibra la señal del controlador regularmente.
- Limpia válvulas en líneas de vapor o agua caliente que puedan generar incrustaciones.
- Cambia actuadores con pérdida de precisión o ciclos lentos.
- Usa actuadores inteligentes con auto-diagnóstico y alarmas.
CONTENIDO ÚTIL – Válvulas Sanitarias Definox de Alta Durabilidad
5. Paradas recurrentes o no planificadas: el síntoma final
Cuando varias de las señales anteriores no se detectan a tiempo, el desenlace es inevitable: interrupciones del proceso productivo. Ya sea por una válvula bloqueada, una fuga grave o una falla hidráulica, estas paradas tienen un alto costo.
Costos ocultos de las paradas por fallas de válvula
- Horas-hombre perdidas en reparación urgente
- Penalizaciones contractuales por incumplimiento de producción
- Riesgo de accidentes por sobrepresiones o derrames
- Reputación afectada ante clientes o auditores
Cómo prevenirlas
- Implementa un programa de mantenimiento preventivo con inspección, limpieza y calibración.
- Registra y analiza datos de caudal, presión y posición con herramientas de diagnóstico predictivo.
- Sustituye válvulas antiguas por modelos con diagnóstico digital (HART, Foundation Fieldbus).
- Capacita a tu personal para detectar estas señales a tiempo.
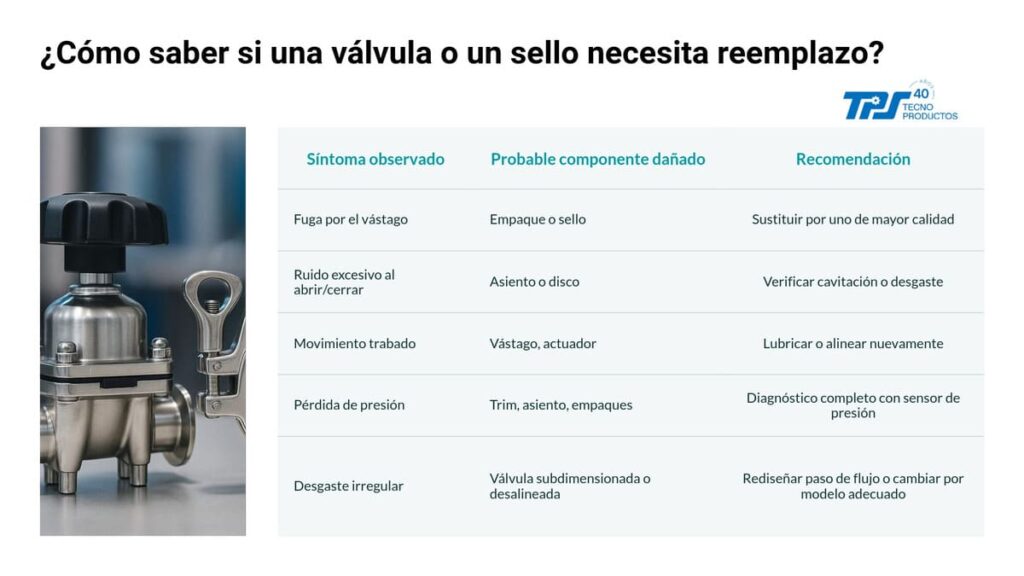
¿Cómo detectar el momento ideal para reemplazar una válvula o un sello?
Aquí te dejamos una tabla práctica:
Síntoma observado | Probable componente dañado | Recomendación |
---|---|---|
Fuga por el vástago | Empaque o sello | Sustituir por uno de mayor calidad |
Ruido excesivo al abrir/cerrar | Asiento o disco | Verificar cavitación o desgaste |
Movimiento trabado | Vástago, actuador | Lubricar o alinear nuevamente |
Pérdida de presión | Trim, asiento, empaques | Diagnóstico completo con sensor de presión |
Desgaste irregular | Válvula subdimensionada o desalineada | Rediseñar paso de flujo o cambiar por modelo adecuado |
Recomendaciones para un Plan de Mantenimiento Efectivo
La mejor forma de evitar fallas críticas es actuar de forma anticipada. Aquí un esquema para implementar un plan de mantenimiento de válvulas de control:
- Clasificación por criticidad: Identifica qué válvulas, si fallan, pueden detener tu producción.
- Rutina de inspección visual mensual: Busca fugas, corrosión, ruidos o vibraciones.
- Limpieza interna cada 6 meses: Especialmente en válvulas de vapor, químicos o agua dura.
- Recalibración y lubricación anual: Asegura precisión y reduce fricción.
- Reemplazo predictivo de sellos y asientos: Basado en ciclos de operación y tipo de fluido.
Las válvulas y sellos pueden parecer simples, pero son el corazón del control de procesos industriales. Ignorar sus señales de falla puede traducirse en millones perdidos por paros, reprocesos o incluso accidentes. Por eso, entender las señales de advertencia —y actuar a tiempo— es una inversión crítica para cualquier planta moderna.
Recuerda: más vale intervenir una válvula en parada programada que apagar una línea completa en plena producción.
¿Quieres ayuda para implementar un sistema de diagnóstico predictivo o mejorar tu plan de mantenimiento? Contáctanos. Nuestros especialistas pueden ayudarte a evitar la próxima parada antes de que ocurra.